In our agricultural planting, we must reasonably grasp the production efficiency and use our tractors reasonably so as to make our vehicle braking more flexible, so how should we operate correctly during the operation woolen cloth?
Start
1. After the tractor starts normally, observe the surrounding environment, and after confirming that there is no obstacle, close the door and send a signal.
2. Disengage the tractor clutch, push the shift lever into the appropriate gear, and shift the gear smoothly and accurately.
3. Gradually increase the accelerator while slowly engaging the clutch to make the tractor start smoothly. The process of engaging the clutch should be fast and then slow. After the tractor has moved away, the clutch pedal can be fully released. Do not step on the clutch pedal while driving to avoid early wear of the clutch friction plates
Variable speed
When a tractor is driving, with the change of environmental conditions, it is necessary to continuously change the driving speed. Whether the tractor can shift gears in a timely, accurate and rapid manner has a great influence on prolonging the service life of the locomotive, ensuring smooth driving and saving fuel.
1. Selection of gears
Changing the gear is actually changing the ratio of the engine speed to the transmission shaft speed. The lower the gear, the greater the speed ratio, and the greater the torque and traction. Conversely, the higher the gear, the less torque and traction you get.
During driving, when the movement resistance increases and requires large traction (such as uphill, heavy load, etc.). The low-speed gear should be selected; but the low-speed gear has low vehicle speed, high engine speed, fast temperature rise, and large fuel consumption, so the low-speed driving time should be as short as possible.
The medium-speed gear is a transition gear from low to high or from high to low, and is usually selected when turning, crossing a bridge or when it is difficult to pass. When the road conditions are good and the engine has sufficient power, the high-speed gear should be selected.
High-speed gear travels fast and saves fuel, but traffic safety must be ensured.
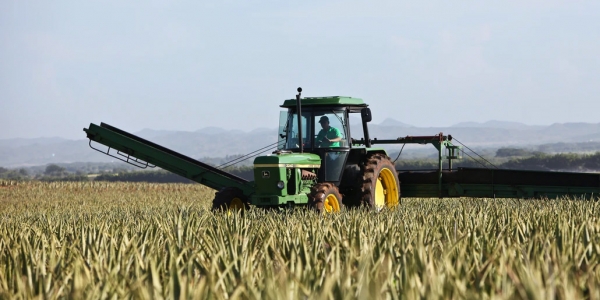
2. The operation of shifting from low-speed to high-speed
1) Refuel to increase the speed (rushing), the rushing should be stable, the rushing time varies according to the load of the locomotive, the rushing time is longer when the load is heavy, and the rushing distance of the high-speed gear is longer than that of the low-speed gear;
2) Lift the accelerator, step on the clutch pedal, and place the gear lever in the neutral position;
3) Engage the clutch, then disengage the clutch and quickly shift the shift lever to a higher gear;
4) Refuel smoothly and shift is completed;
3. The operation of high-speed shifting to low-speed
1) Reduce the accelerator, disengage the clutch, and place the gear lever in the neutral position;
2) Engage the clutch and add empty oil;
3) Quickly depress the clutch pedal, shift the gear lever to a lower gear, engage the clutch, and refuel. The key to this process is to grasp the size of the empty oil, which depends on the speed of the vehicle. When changing the same gear, when the speed is fast, the empty oil should be added more, and vice versa. When the speed is very slow, it is not necessary to add empty fuel.
4. Precautions for shifting
1) When shifting gears, you should concentrate, keep your eyes on the front, hold the steering wheel in one hand and the ball head of the gear shift lever in the other hand, gently push into the required gear, do not look left or right, and do not push or pull hard on the gear lever, so as not to damage the meshing gear;
2) The speed change should be carried out step by step, and the gear should not be exceeded;
3) When changing the forward or reverse direction, the gear should be changed only after the locomotive stops steadily.
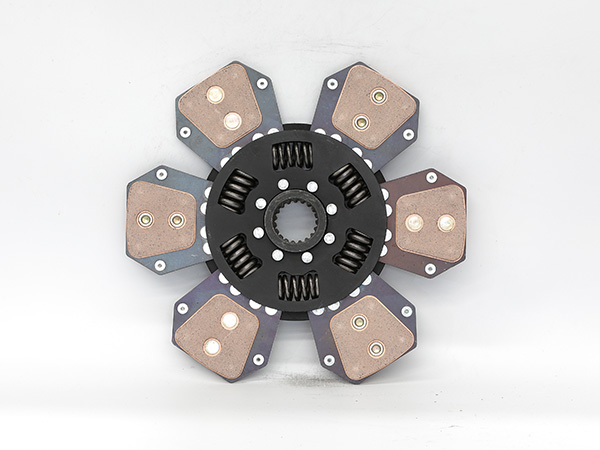
Turn
1. When the crawler tractor is turning, the joystick on the steering side can be pulled to turn. When making a sharp turn, first pull the lever all the way, then depress the brake pedal on that side, and then release the pedal and then the lever after turning.
2. When turning the wheeled tractor, it should decelerate first and then turn. When turning slowly, you should turn early and slow, and hit less and return less; when turning sharply, turn late and fast, and make more turns; when turning small turns, you can use unilateral braking assistance at low speed.
3. When turning, since the wheel tracks of the front and rear wheels on the inside do not overlap, the track of the rear wheel is biased to the inside. Therefore, when turning, don’t get too close to the inside. You should turn the steering wheel appropriately according to the size of the camber and the distance of the roadside obstacle, so that the inside rear wheel can pass smoothly and prevent the rear wheel from crossing the road and encountering obstacles.
Reversing
When reversing, keep your mind focused, use a low-speed throttle, and be ready to park at any time.
Brake
1. Braking method of tractor
One is engine braking and the other is braking with the brakes. Engine braking is to use the drag effect of the engine to brake, that is, when the speed of the vehicle is high, the accelerator is rapidly reduced, and the compression force of the cylinder is used to brake the driving wheels to achieve the purpose of reducing the speed of the vehicle.
Tractor braking is divided into two types: predictive braking and emergency braking according to its nature: predictive braking is to make judgments in advance according to terrain, environment, etc., to decelerate and stop in preparation, and the method is to reduce the “accelerator”, Use engine braking to reduce speed. If necessary, use the brake to brake intermittently at the same time. After the vehicle speed is reduced to a certain level, disengage the clutch and use the brake to stop the vehicle. In special circumstances, the brake pedal should be quickly stepped on, and then the clutch should be disengaged to stop within a short distance. When emergency braking, do not depress the clutch pedal first
2. Parking
When parking, choose a suitable location to ensure traffic safety. Decrease the accelerator to reduce the speed of the tractor, then depress the clutch pedal, place the shift lever in neutral, or lightly depress the brake pedal to assist in stopping. After the car is stopped, the engine should be idled, and the engine should be turned off when the engine temperature drops below 60°C. If the load of the tractor is light, the working time is short, and the engine temperature is not high, it can be turned off after stopping.
The above is all about the correct operation of the tractor. The tractor driver must master some necessary driving skills in the process of driving the locomotive, which is very important for the normal use of the tractor and the service life of the tractor gift box IQ. At the same time, it can also improve work efficiency, reduce unnecessary economic losses, and provide the most basic security guarantee for the safety of oneself and others.