The so-called clutch is to use “off” and “on” to transmit the right amount of power. The agricultural machinery clutch consists of friction plates, spring plates (disc springs are used for tractors, and diaphragm springs are used for harvesters), a pressure plate and a power output shaft. It is transmitted to the gearbox to ensure that the agricultural machinery transmits the appropriate amount of driving force and torque to the driving wheels under different working conditions.
The clutch is a device that connects the agricultural machinery engine and the transmission, and the clutch pedal is the clutch control device. When the clutch pedal is stepped on or lifted, the engine and the transmission will be temporarily separated or smoothly combined to cut off or transmit power to realize changes in the agricultural machine’s starting, shifting, parking and other motion states. Slowly lift the clutch until it is fully lifted. If the engine stalls when the clutch is lifted, it proves that the clutch is not slipping. If the engine does not stall when the clutch is lifted, it may be a problem with the clutch.
Tractor clutch
The tractor clutch generally uses a double-acting clutch, that is, one road is responsible for walking, and the other road is responsible for power output. Due to structural reasons, the gap between the flange of the clutch pressure plate and the housing is relatively small, especially in the south of the Huaihe River in my country, where there is abundant rainfall and high air humidity, and the tractor is not used every day (sometimes it is not used for several months) , In this way, it is bound to be prone to rust, which will cause adhesion between the pressure plate bracket and the flange, resulting in incomplete separation of the clutch.
Suggestion: before using the tractor parked for a long time, the tractor operator should first open the clutch inspection port, use a flat screwdriver to turn the clutch assembly, and spray a little rust remover on the three flanges of the clutch pressure plate, and then step on the A few clutch pedals make it move back and forth, and then the tractor can be used normally for various tasks.
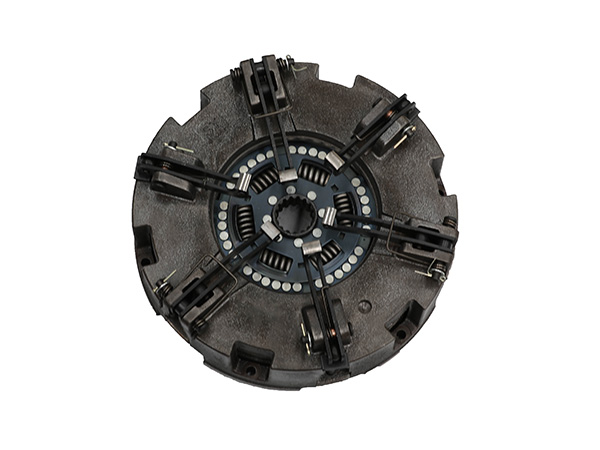
Combine Harvester Clutch
Because the working environment of the combine harvester is very bad, there is a lot of dust in the air, and the clutch is an open structure. When the harvester is working, the dust in the air is brought into the clutch chamber from the gap between the clutch pulley and the clutch housing support, and is captured. The rotating clutch is driven by the centrifugal force to the inner space of the pressure plate, gradually forming the phenomenon of clutch slippage (the combine harvester will appear weak when walking). In addition, the clutch drive belt of the combine harvester should not be too tight and should not be started at high speed, otherwise, serious faults such as bending of the clutch shaft will easily occur.
Suggestion:
1. The designer of the Technology Center Research Institute should design grooves on the inner wall of the clutch housing (corresponding to the clutch pulley), and stick felt strips of uniform thickness to prevent large dust particles from entering the clutch chamber. Note: rubber seals cannot be used. ring, because the clutch pulley is at the end of a shaft, there will be a large jump).
2. The operator of the combine harvester does not regularly maintain the clutch.
Operation and use of the clutch
First of all, the pedal should be pressed firmly with the sole of the left foot, and the clutch pedal should be stepped down or lifted with the flexion and extension of the knee joint and hip joint. Do not use the toe, sole or heel to step on the clutch pedal to prevent insufficient pedaling force or slipping off. pedal. The action of depressing the clutch pedal should be fast, and all the way to the end, so that the clutch can be completely disengaged, when the clutch pedal is lifted. It should be determined according to the operating situation. Generally, when the working gear is changed to neutral, the clutch pedal can be lifted quickly. When the agricultural machine starts or shifts, the free travel before the off-table device is not engaged can be slightly faster. When the clutch starts to engage Then stop for a while, then slowly lift the clutch pedal (and gradually increase the throttle), and after the clutch is fully engaged, you should quickly remove your foot from the pedal and place it under the pedal. When the clutch is not used during agricultural machinery work , do not put your foot on the clutch pedal! ! ! In order to avoid the half-linkage phenomenon of the clutch, which will affect the transmission torque and increase the wear of the parts.
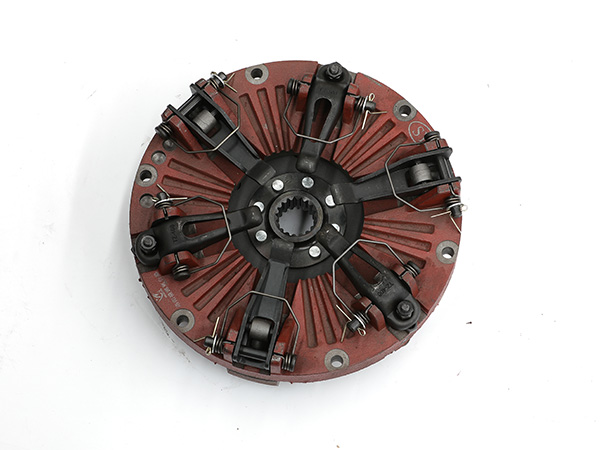
1. Starting and shifting of agricultural machinery:
When starting, depress the clutch to completely disengage; when lifting the clutch pedal, operate according to the essentials of “one fast, two slow, three linkage”. That is, the process of pedal lifting is divided into three stages, starting to lift quickly; when the clutch appears half-linked (the engine sound changes at this time), the speed of pedal lifting is slightly slower; from half-linked to fully combined, the pedal is slowly lifted. Lift slowly. While the clutch pedal is lifted, gradually depress the accelerator pedal according to the engine resistance to make the agricultural machine start smoothly. The operation of the throttle should be smooth and appropriate. The clutch pedal operation method of one fast, two slow and three fast should be followed, and strive to engage smoothly.
2. Reduce clutch usage:
If the temperature is too high, the friction lining will be worn or cracked rapidly. Therefore, minimize the number of clutch disengagement and engagement, and the number of semi-linkages.
3. During emergency braking or approaching a stop:
During the driving of agricultural machinery, do not depress the clutch pedal under any other circumstances except that the clutch pedal must be depressed for braking at low speed (above 10km/h). Depress the clutch and let the agricultural machine coast to slow down to reduce the impact on the engine and drive train.
4. For your safety:
It is strictly forbidden to go uphill and disengage gear, go downhill and step on the clutch to slide in neutral gear, put in gear and lift the clutch pedal to start the engine; it is strictly forbidden to use the method of suddenly accelerating the accelerator and suddenly lifting the clutch pedal to drive the wheels to slip on soft roads, muddy roads, and ice and snow roads. road section.
5. Don’t step on the clutch if you have nothing to do:
When the clutch on the agricultural machinery is working normally, it is in a tightly engaged state, and the clutch should not slip. The separation of the clutch is controlled by stepping on the clutch pedal. When driving, do not step on the clutch pedal at any other time, except that the clutch pedal needs to be stepped on when the agricultural machinery starts, shifts gears and brakes at low speed.
Step on the clutch at work or put your foot on the clutch pedal for a long time, so that the clutch is often in the state of engagement, separation or half-slip, which accelerates the wear of the clutch friction plate and pressure plate, and makes the power of the engine unable to be fully transmitted. To drive the wheels, resulting in traffic costs oil, waste cars, increase traffic costs.
If you put your foot on the clutch pedal for a long time during work, it is easy to cause clutch slippage, clutch disc ablation, etc., and in severe cases, it may even cause ablation and strain on the clutch pressure plate and flywheel end surface, and annealing of the clutch compression spring.
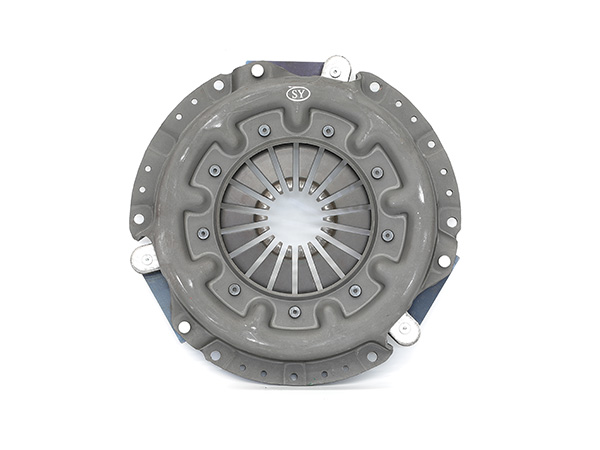
6. Correct operation when shifting gears:
The gearboxes of agricultural machinery generally adopt the shifting structure of meshing sleeves. In order to make the shifting smooth and reduce the wear of the shifting mechanism and clutch of the transmission, the “two-leg clutch shifting method” is advocated. That is, when upshifting, press the clutch pedal while shifting the shift lever to a higher gear; when downshifting, step down the clutch pedal while shifting the shift lever to neutral, lift the clutch pedal and accelerate appropriately according to the vehicle speed. Kick off the gas, then depress the clutch pedal again while shifting the gear lever to a low gear.
7. The correct use of the clutch when braking:
During the driving of agricultural machinery, do not depress the clutch pedal under any other circumstances except that the clutch pedal must be depressed for braking at low speed (above 10km/h). Because when the agricultural machinery is braking at medium and high speeds, depressing the clutch pedal will not help at all to improve the braking ability of the agricultural machinery, and will also bring danger to driving safety.
When braking and parking at low speeds, the purpose of depressing the clutch pedal is only to prevent the engine from stalling. At this time, the correct control method is to depress the brake pedal first, and then depress the clutch pedal to make the agricultural machine stop smoothly.
The use of agricultural machinery clutches is introduced here. In order to enable everyone to correctly use combine harvesters, tractors, etc. to drive agricultural machinery, operate and maintain clutches correctly, so that agricultural machinery can be used for a longer period of time and cost less maintenance costs, integrated for decades. The technical guidance listed in the experience of using, operating and maintaining agricultural machinery, I hope it can be helpful to everyone.